在工业 4.0 时代,设备运维正经历从被动响应到主动预防的革命性转变。预测性维护技术通过对设备状态的实时监测与智能分析,显著提升了运维效率。其中,剩余使用寿命预测(RUL)与根本原因分析(RCA)模型的协同应用,成为优化设备运维的关键技术路径。
预测性维护通过物联网传感器、大数据分析与人工智能算法,构建设备健康状态的动态画像。其技术体系包含三大核心模块:
状态监测系统:部署振动、温度、压力等多模态传感器,实现设备运行数据的高频采集。例如,某汽车工厂在冲压设备上安装 128 个振动传感器,每 20ms 采集一次数据。
智能分析平台:运用机器学习算法对数据进行特征工程,提取包括时域统计量(如峰峰值)、频域特征(如 1x 转频幅值)和时频域特征(如小波能量熵)等关键指标。
决策支持系统:基于 RUL 预测结果与 RCA 分析结论,生成差异化的维护策略。某石化企业通过该系统将计划外停机率降低了 42%。
RUL 预测模型通过建立设备退化轨迹与寿命周期的映射关系,实现剩余寿命的精准估算。其技术实现包含四个关键步骤:
退化特征选择:采用互信息法筛选与寿命高度相关的特征。例如,某风力发电机轴承 RUL 预测中,峭度值与寿命的相关性达 0.87。
退化趋势建模:应用粒子滤波算法拟合退化曲线。某案例显示,该方法较传统线性回归预测误差降低 35%。
不确定性量化:通过蒙特卡洛模拟生成 RUL 置信区间。某航空发动机涡轮叶片预测结果显示,95% 置信区间宽度小于 150 小时。
维护阈值设定:结合设备重要性等级设定触发阈值。某半导体光刻机设定 RUL<200 小时时自动触发维护流程。
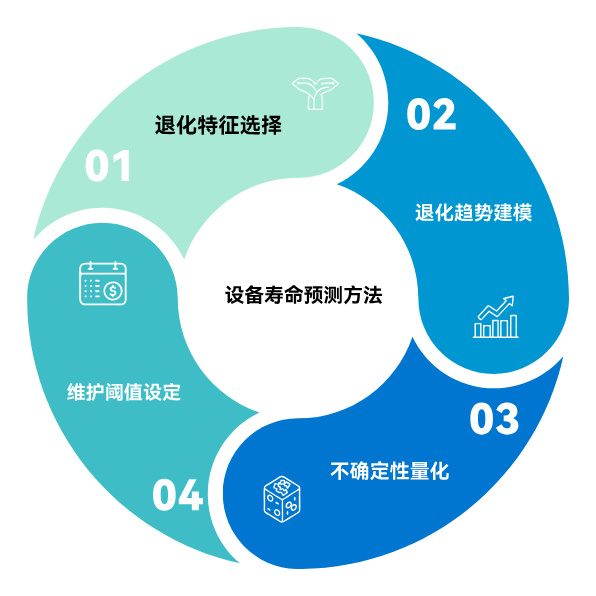
RCA 模型通过因果推理分析,定位设备故障的根本原因。其技术框架包含三大模块:
故障树构建:基于 FMEA(失效模式与影响分析)建立层次化故障逻辑关系。某案例构建的数控机床主轴故障树包含 6 个一级原因、28 个二级原因。
因果关系挖掘:采用贝叶斯网络学习变量间依赖关系。某案例发现进给轴振动异常与丝杠预紧力不足的条件概率达 0.73。
根本原因定位:运用 Dempster - Shafer 证据理论融合多源证据。某案例综合振动、温度、电流数据,定位轴承游隙过大为根本原因。
RUL 与 RCA 模型的协同应用形成闭环管理,实现运维效率的倍增效应:
维护策略动态调整:
资源优化配置:
知识沉淀机制:
某跨国制造企业实施 RUL 与 RCA 协同系统后,取得显著成效:
指标 | 优化前 | 优化后 | 提升幅度 |
---|
计划外停机时间 | 12.7h / 月 | 4.1h / 月 | 67.7% |
维护成本 | 185 万元 / 年 | 112 万元 / 年 | 39.5% |
故障平均修复时间 | 8.2h | 3.5h | 57.3% |
备件周转率 | 2.1 次 / 年 | 3.8 次 / 年 | 81.0% |
典型应用场景包括:
某钢铁厂连铸机 RUL 预测将更换周期从固定 6 个月优化为动态 9-12 个月
某制药厂反应釜 RCA 分析定位搅拌轴断裂根本原因为润滑脂选型错误
某港口起重机 RUL 预测系统实现预防性维护覆盖率从 32% 提升至 89%
当前技术仍面临多方面挑战:
小样本学习:设备早期故障数据匮乏影响模型精度
实时性要求:需在 50ms 内完成 RUL 预测与 RCA 分析
多模态融合:融合振动、油液、工艺参数等多源数据
可解释性需求:维护人员需要理解模型决策逻辑
未来发展趋势包括:
边缘智能:将 RUL/RCA 算法部署至边缘计算节点
数字孪生:构建虚拟设备与物理实体的实时映射
联邦学习:跨企业协作训练模型保护数据隐私
自进化系统:模型自动更新故障特征库
预测性维护技术的深化应用,正在重构工业设备运维的价值逻辑。通过 RUL 与 RCA 模型的协同创新,企业不仅能实现运维成本的显著降低,更能构建设备全生命周期的健康管理体系。随着人工智能与物联网技术的持续突破,预测性维护将向更高层次的自主决策迈进,为智能制造的可靠性保障提供终极解决方案。